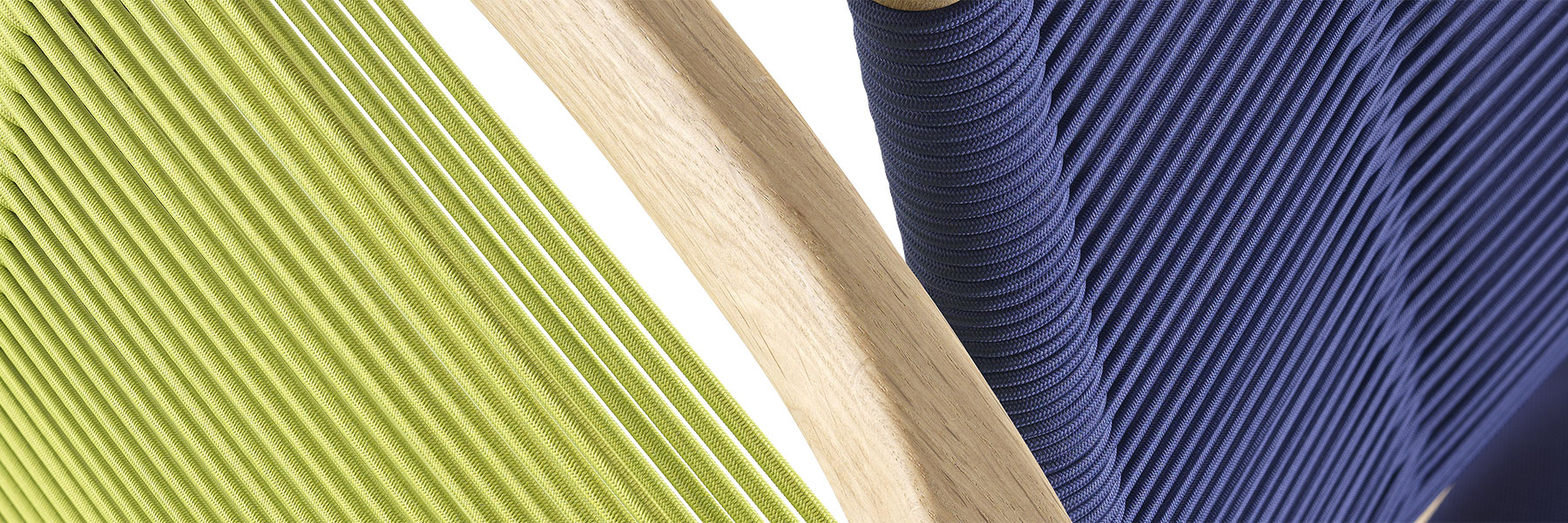
Case history
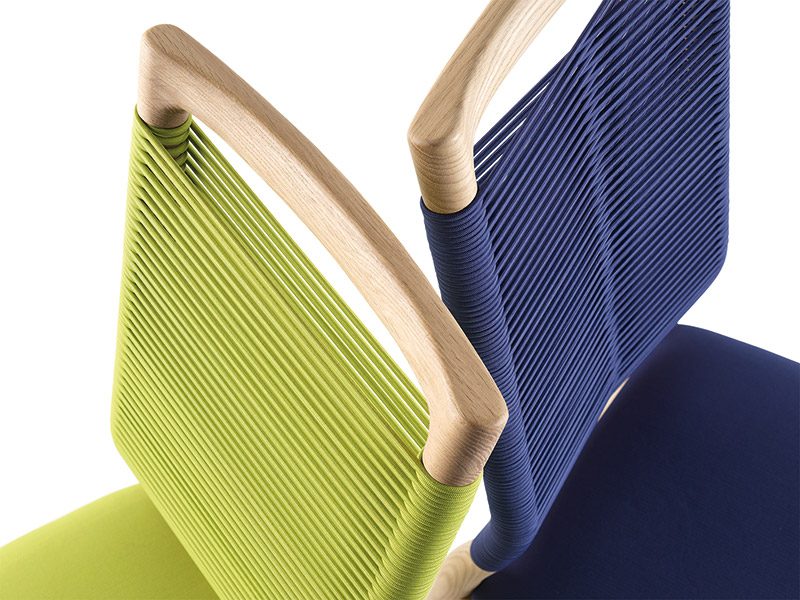
Hidden solutions that permit the necessary support
The requirement for this model was that of respecting the lightness that it expresses, by solving the problem of the structure’s resistance. The forty meters of cord as a matter of fact generate a great deal of stresses that are added to those of the person who is sitting. The solution we delivered in the end produced the desired result thanks to special joints and hidden solutions that allow the necessary support without losing the slim thicknesses and original shapes.
Slim thicknesses and original shapes
The largest contribution to this project is one that is completely invisible, and this is our success. It is complex work of engineering that makes it possible to respect the designer’s commitment that bestows sinuous shapes to the eye, comfort to the body and the necessary ergonomics and during testing, provides the chair with resistance to severe fatigue and load testing. One task of no small importance was that of strengthening the chair and distributing the forces generated on the part of the rear leg that is developed with a helical shape, which is then joined with the padded backrest. We likewise distributed the pressures removing the load form the most fragile points and stably joining the back to the legs, without any screws or visible components.
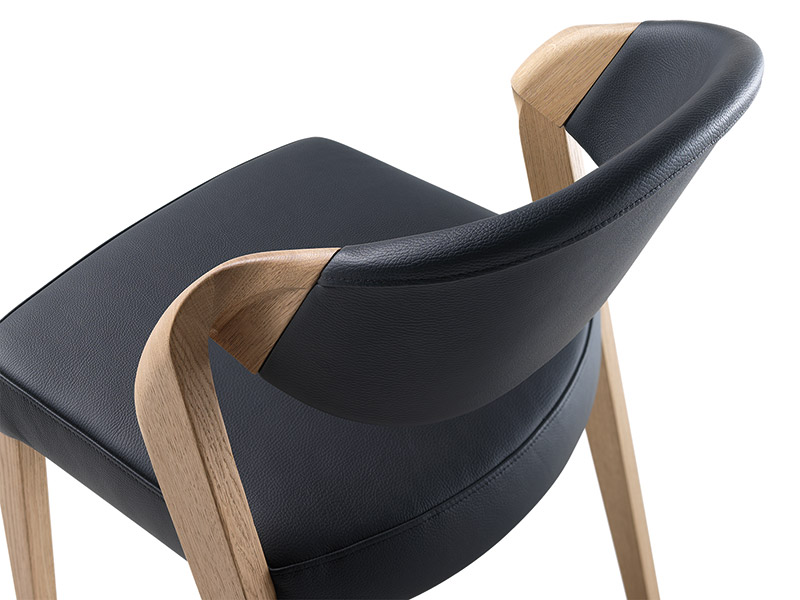
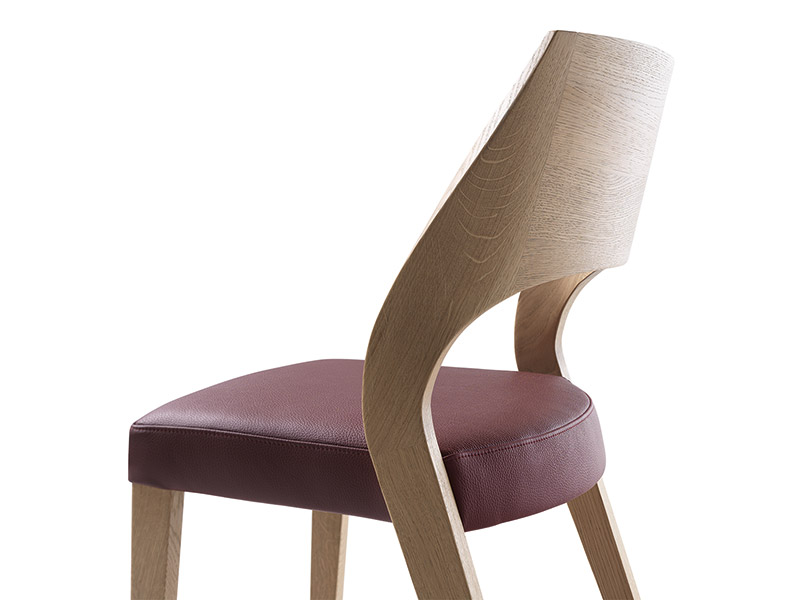
Broad back without screws or fastening elements
In order to create the broad back of this model it has been necessary to combine and shape the eight pieces that comprise it. This required careful analysis and evaluation of the forces of each element because they each generate thrusts and resistances. Each one of these parts was machined using 5-axis CNC machines resulting in soft and sinuous shapes with an original design. The fastening of the backrest to the seat required a careful evaluation in order to avoid screws or visible components, while maintaining the design’s thicknesses and spaces.
An exciting challenge
This ambitious product was initially conceived to be made in plastic materials, however the high manufacturing costs involved almost led to the choice of giving up on the product. We were contacted to find a solution and we found it by using wood. The particularly thin layers and design that exalted the lightness drove the study to its utmost, driving us to find ways to give life to this chair. Guaranteeing the 24x24mm section of the legs and back, and at the same time the necessary stability, proved to be an exciting challenge, also adding to this the beauty of wood.
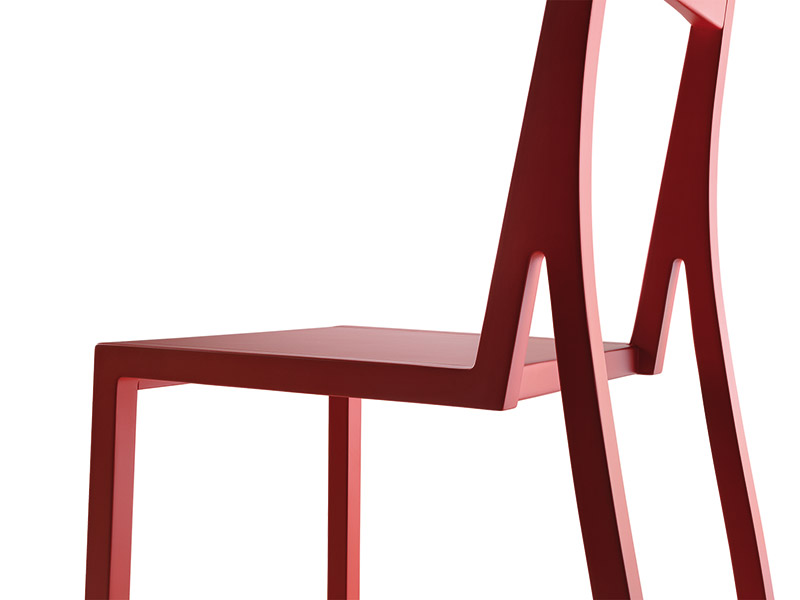
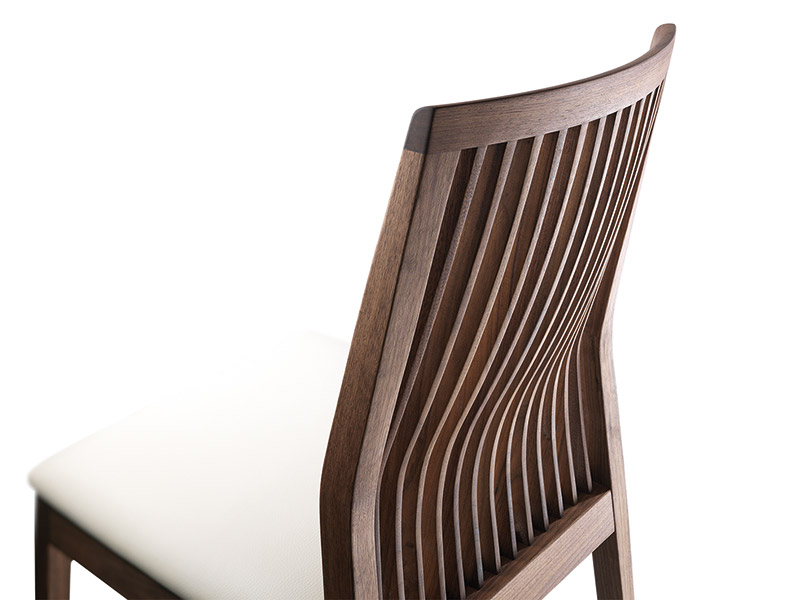
Thirteen slats with variable sections and shapes
At first sight the back of this chair generates a strong interest owing to its extraordinary complexity within a well-balanced design whole. The thirteen slats have all variable sections and shapes, in order to ergonomically follow the human back we conceived of a rhomboidal base that followed a different helical positioning for each slat depending on its position. A great deal of passion and various laboratory tests were required to realize this complex design, to make the product both solid as well as cost effective to manufacture. The manufacturing of this model is carried out with the use of 5-axis CNC woodworking machines.
Push beyond the normal possibilities
Our customers know that with us it is possible to push beyond the normal possibilities and broaden the frontiers of design, certain of always being able offer new shapes together with the same high-quality standards. This is what happened to this chair from particularly thin body and curved design. Normal materials proved to be inadequate in the resistance tests, so we found high density laminated woods with an innovative patent that thanks to a micromachining are able to provide us with extraordinary capabilities. The ability to customize upholstery makes this a very popular model, that is beautiful even in its all-wood versions either with all of the wood exposed or with the front upholstered and the back exposed.
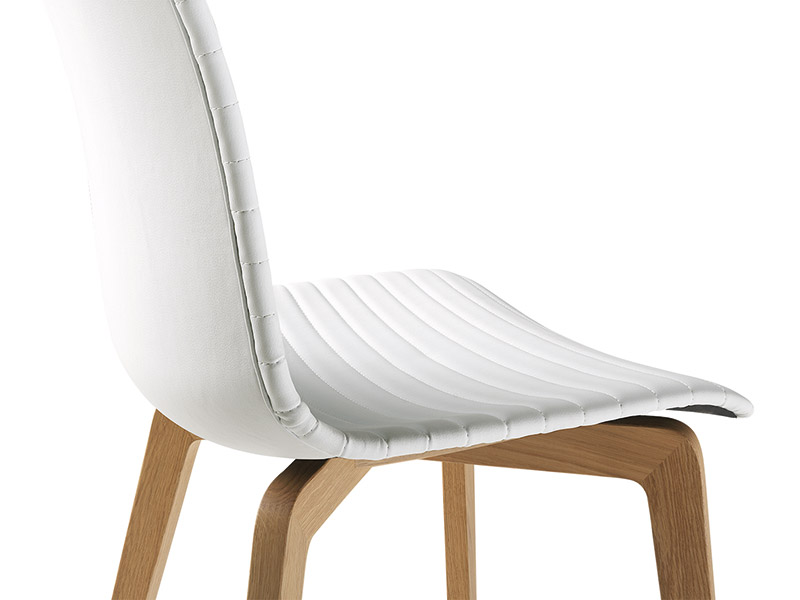
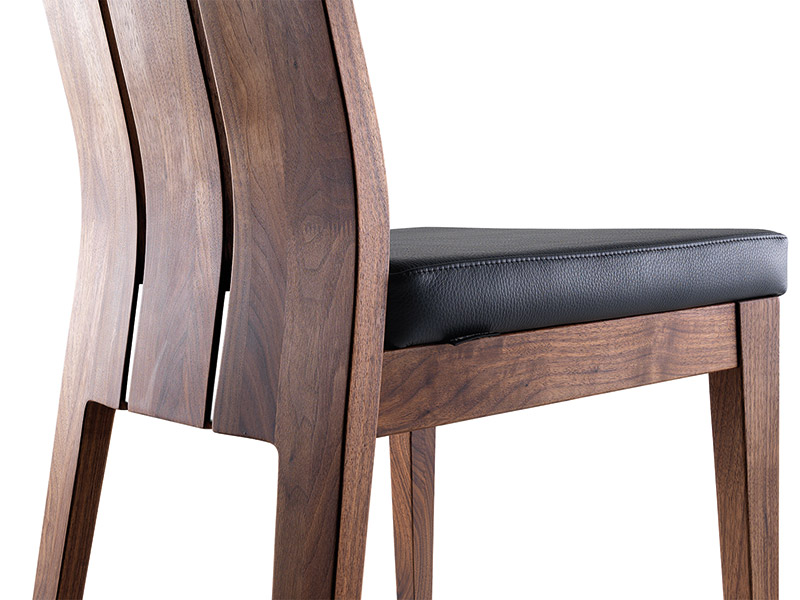
Keeping abreast with trends is not always uneconomical
Sometimes keeping abreast with trends requires solutions that seem impossible or uneconomical. Not for us. Several different tests were needed in order to create the angular curves of this back, but all of these tests were beyond what the wood can physically withstand. We cut so the piece without losing the continuity of the wood grain, while managing to maintain the production costs. The result is a chair with a strong personality and stability, while the insertion of metal elements helps to give it charm and style.
Making something easy that is not so
Apparently this chair looks simple and straightforward, but for us nothing is as it seems, there is always a great deal research that goes into making something easy that is not so. Leading edge machinery was used to give it the right curvature, a thickness that becomes ever more slender, the hollow space in the centre with a radius gradually thins as it goes upwards and that sense of modernity and formal rigor. The vertical slats that make up the backrest are designed to be able to withstand stresses without cracking. The chair is then characterized by a surface scratching and oiling process that has enjoyed a great deal of success.
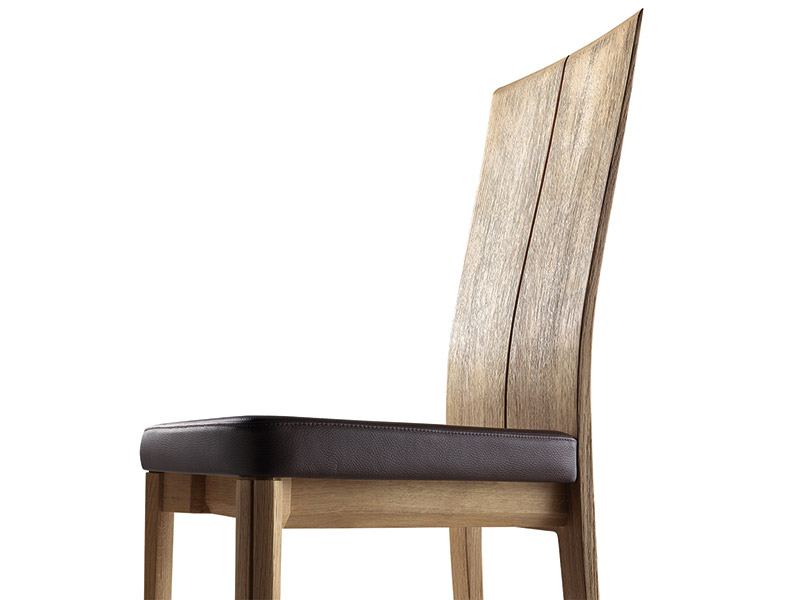
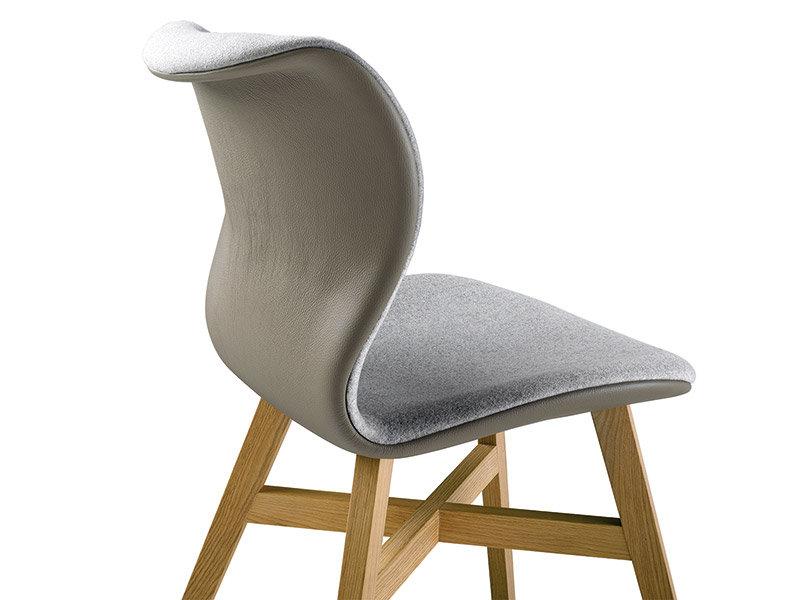
Two wood bodies, built with CNC milling machines
For the realization of this project we designed the two wooden bodies in 3D and built the pressing moulds of the same with 5-axis CNC milling machines. In this case, there are two wood bodies and these are fitted together in the middle, thus creating two different surfaces on the outside that can be customized with different kinds of upholstery. Specific machines allows us to cut the cloth or the leather according to the thickness or elasticity in order to adapt it perfectly to the structure.
Taking full advantage of the technical possibilities
The request of the designers was to give stability to the daring inclinations of this chair. For us, it was the start of a new adventure. With only a few millimetres to condense most of the stresses of the chair and as always, there must be no reinforcement in view. Every detail of this model takes full advantage of the technical possibilities for a result of strong aesthetic impact, without sacrificing the cleanliness of the lines.
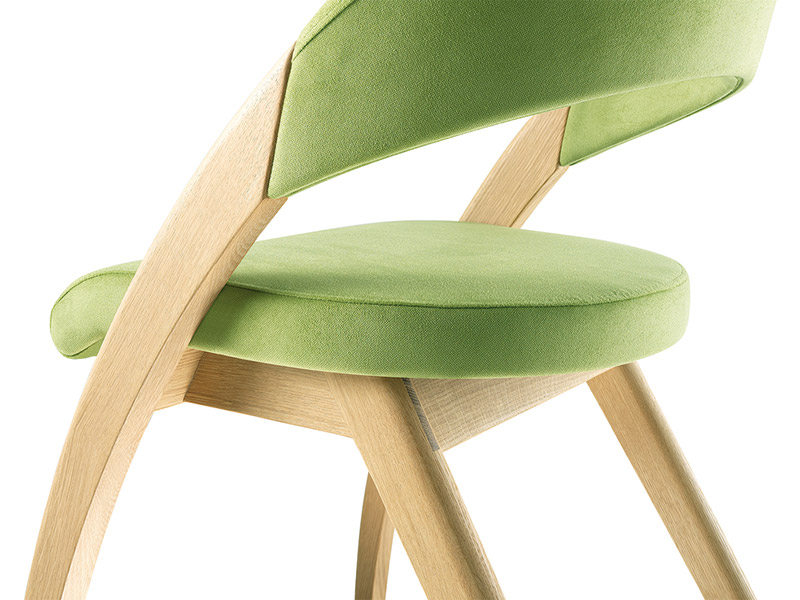
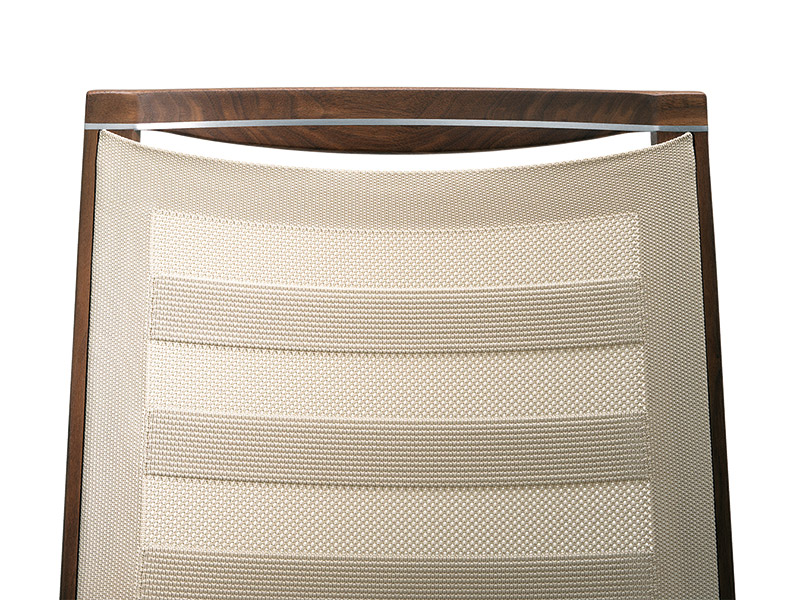
Assembling different materials together
Assembling different materials together is a trend that is increasingly gaining strenght. We try to bring cutting-edge solutions, working on thickness, joints and specific adhesives that seem like magic, but instead cloaks a high engineering effort together with original solutions designed for the individual product. In this case we have designed a special machine from scratch for the insertion of the elastic cloth in wooden structure. Even the use and assembly of the aluminium profile required a complex reasoning process in order to bring the thickness of the lower back of the chair to thin down to some tenths of a millimetre before almost disappearing in the aluminium.
Mission was accomplished without any reinforcement or screw in view
An essential and light design for this model that has been developed in different variations. In addition to the development of the particular curvature of the arms and the body, the request was that of obtaining stability, resistance to fatigue and impact using thicknesses and sections that ere reduced to a minimum. In this case as well, the mission was accomplished without any reinforcement or screw in view, conferring an image of high quality and elegance the to project.
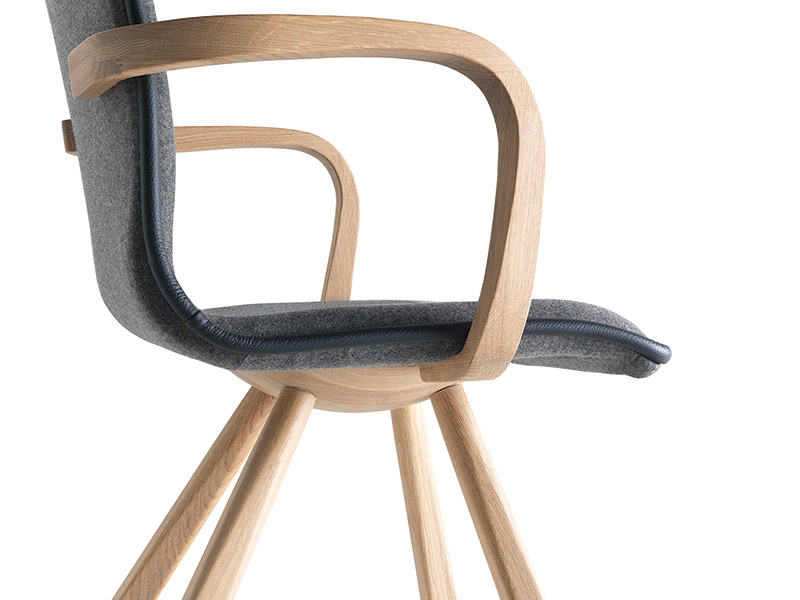
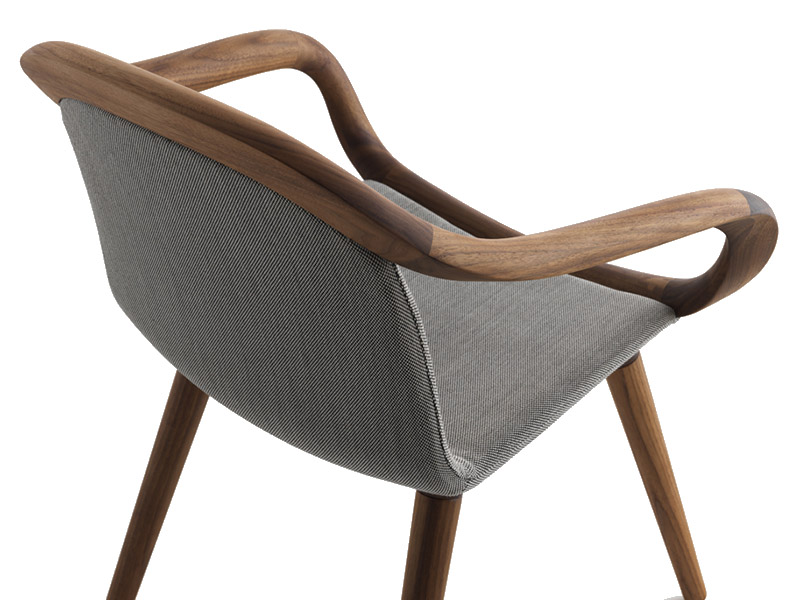
Design beyond measure.
The line that accommodates the seat is seamless; the tactile sensation along the profile is extraordinary. No screws, just a clever interplay of joints to accommodate, support and distribute weights proportionately. Bodywork customisations are endless and the precise and careful creation of the stem is entrusted to our numerical control machines operating on five axles.